Advantages/Disadvantages of Carbon Ceramic Brake Disk Refurbishment Technology
General
The production of carbon ceramic discs from C/C-SiC using the method of infiltration with liquid silicon (LSI – liquid silicon infiltration) includes the process of hot pressing of the carbon matrix (carbon fibers and resin), during which the basic structure/shape of the disc is prepared. Using LSI technology, liquid silicon is infiltrated into the matrix, which forms SiC (silicon carbide) – ceramics, together with carbon fibers at high temperatures.
The carbon fibers in the disc structure give the disc high strength, which enables high mechanical loads on the disc. The “ceramic” part of the structure primarily increases the hardness, especially of the upper surface, which enables low disc wear and a long service life.
This technology (LSI) is used by the leading SGL manufacturer Brembo.
You can find out more about making discs here.
Disadvantages of disks made using LSI technology Carbon Ceramic Brake Discs
Uncontrolled or non-random distribution of silicon around the disc circumference
The uneven distribution around the circumference results in a difference in density/mass/hardness of the disc around the circumference. During the production process, the manufacturer excludes bad discs from the process, and most of them do not reach the customer.
Unfortunately, 100% control is not possible and “quality borderline” discs can reach customers. In such cases, even when the discs are dimensionally adequate, due to the uneven structure of the disc, even during normal use, vibrations or noise can occur.
Such discs are also more sensitive to shape deformation (twisting), which impairs braking ability.
Photo is original located here.
Cracks (CCB discs – Porsche, Mercedes, Audi…)
The top layer of the disc is extremely hard, but not hard/tough like the carbon fiber base. The layers expand/contract differently at elevated temperatures and as a result of temperature loads on the disc (in case of strong braking) the top layer cracks. This can be seen as micro-cracks on the surface, which is possible even with almost new discs.
The result of the cracks is an open structure of the disk, which accelerates the passage of oxygen into the core of the disk oxidation/combustion of carbon fibers. As a result, the discs wear out faster and lose the mechanical strength required under high performance.
Delamination
When the performance is increased, the layers stretch differently and as a result micro-cracks occur between the layers.
In the case of an increase in micro-cracks, delamination of the top layer from the base may occur under high performance.
In this case, the braking ability is reduced due to the reduced working surface of the disc and, in extreme cases, the disintegration of the disc structure may occur. Such a disk must be restored or replaced immediately.
Most defects on carbon discs (oxidation and delamination) can be effectively repaired.
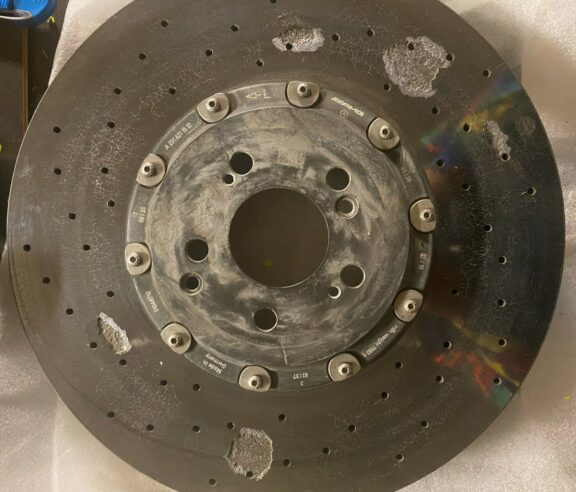
Delimination CCB discs ReDisc
Most defects on carbon discs (oxidation and delamination) can be effectively repaired.
Methods of Carbon Ceramic Brake Disc Refurbishment
There are two methods in the market by which the disk can be recovered.
- LSI technology follows the same process as production and uses silicon for infiltration, which reacts with carbon fibers to form SiC (ceramics) at elevated temperature.
- LPI technology uses different polymers and pyrolysis for infiltration. The polymer contains the basic components (Si and Carbon) for the formation of ceramics (SiC) at an elevated temperature. (used by ReDisk d.o.o.).
The two methods differ from each other in terms of technological parameters, which affect the quality of the performed refurbishment.
Below presents the main features/differences when using each refurbishement method.
METHOD LPI (ReDisc) | |
Difference | The polymer protects (coats) the existing carbon fibers and fills the air pockets. |
Retention of carbon fiber allows for high disc strength, and Silicon Carbide (ceramic) fills the air pockets, increasing strength/hardness and disc life. | |
The disc is additionally protected with an OXY coating on the surface, which makes it difficult for the carbon fibers to oxidize and thereby further extends the life of the disc. | |
Figure 1 | |
Advantages | The strength of the disc increases. |
The open porosity on the surface is reduced, the hardness remains the same as before restoration. | |
The carbon fiber is protected, thus slowing future disc wear. | |
Proven technology – more than 500 remanufactured discs on the market. | |
Weaknesses | Due to multiple cycles of infiltration and pyrolysis, a longer production time is required. |
Dangers | / |
METHOD LSI | |
Difference | The high temperature of molten silicon reacts with carbon in the form of carbon fibers. Thus, the amount of carbon fiber is reduced and replaced by SiC (ceramic). |
This method increases the hardness of the material, and due to the reduction of carbon fibers, the strength of the disc, which is crucial for mechanical stability or high loads. | |
Open porosity (microcracks on the surface) also increases, reducing the life of the disc. | |
Figure 2 | |
Advantages | Hardness increases. |
The possibility of creating a new layer (increasing the thickness of the disc). | |
Weaknesses | The strength, which is crucial for the mechanical stability of the disc, is reduced. |
Unproven restoration technology. | |
Dangers | Due to the decrease in strength, the risk of disc deformation increases with increased discload (see figure).![]() |
Figure 1: LPI (ReDisc) technology protects the carbon fiber and fills the air pockets with SiC (ceramic).
Figure 2: LSI technology…Silicon reacts with carbon fibers to form SiC (ceramic).
Black carbon Fibers react with Silicium and turn into SiC (ceramic). More info you can find here
Conclusion of refurbishment technology Carbon Ceramic Brake Disc
Increased wear (faster than normal) or disc damage is caused by unstable/uncontrolled LSI disc production (described above).
It is inefficient/pointless to use the same technology as for production to restore or improve a worn disc, as with each new process we partially increase the hardness of the disc but at the same time reduce the strength of the disc, as it uses carbon fibers in the process. The strength, however, is crucial for the stability of the disc and prevents the disc from disintegrating under increased load. At the same time, we introduce additional instability into the process (Si infiltration into the disk).
The use of LSI technology for the refurbishment process increases the sensitivity of the disk to higher loads, where it can also fail (blow it up).
Based on these findings/testing, LPI technology was developed, which is the fruit of several decades of research and testing by Mr. Miklavža Zornik in connection with the Jozef Stefan Institute and the Faculty of Mechanical Engineering of the University of Ljubljana under the leadership of dr. Kristoffer Krnel and Dr. Mitjan Kalin from Slovenia, Germany and America.
Refurbishment using LPI technology has an exclusively positive effect on the disc and does not deteriorate any of the mechanical properties of the disc. The mechanical hardness of the surface remains the same as before resurface or increases slightly, while the strength of the disc increases.
Trust the proven LPI refurbishment technology, which has produced more than 500 pieces and is used by ReDisc d.o.o..
Team ReDisc d.o.o.